Technology
Production
Reproduction
With its professional staff, KİMPACK is able to provide all pre-press services such as cromolyn and cliche within its own structure. In this regard, the latest possibilities of technology are used.
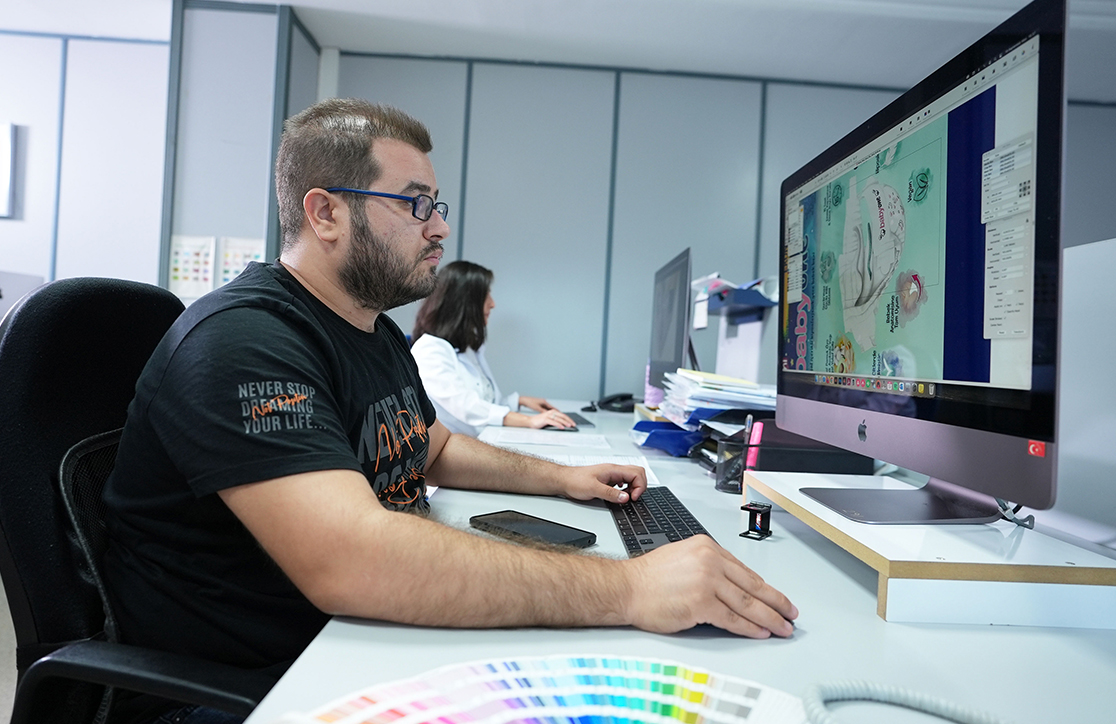
Cliche
In 2001, the clichés needed by the printing machines started to be produced in KIMPACK Plastik facilities. In this department, which consists of graphic and cliché manufacturing departments, the latest developments in technology are closely followed. The studies coming from the customers are given to the printing company by converting them into clichés according to the flexo printing technique requirements. It is a matter that requires attention, patience and technology to turn the designs that our clients' agencies are working on into a cliché. Therefore, we perform graphic works with our experienced graphic designers, using the best software. The most important advantages of making our cliché in our own structure are; to ensure the improvement of print quality and to prevent the works of our customers from being heard before the product is released to the market.
As of 2022, XPS Crystal, the world's top innovation, completed and added the plate technology investment, which optimally combined UV and back exposure in a single machine. In this way, the highest level of screen quality has been achieved with the flexo printing technique.
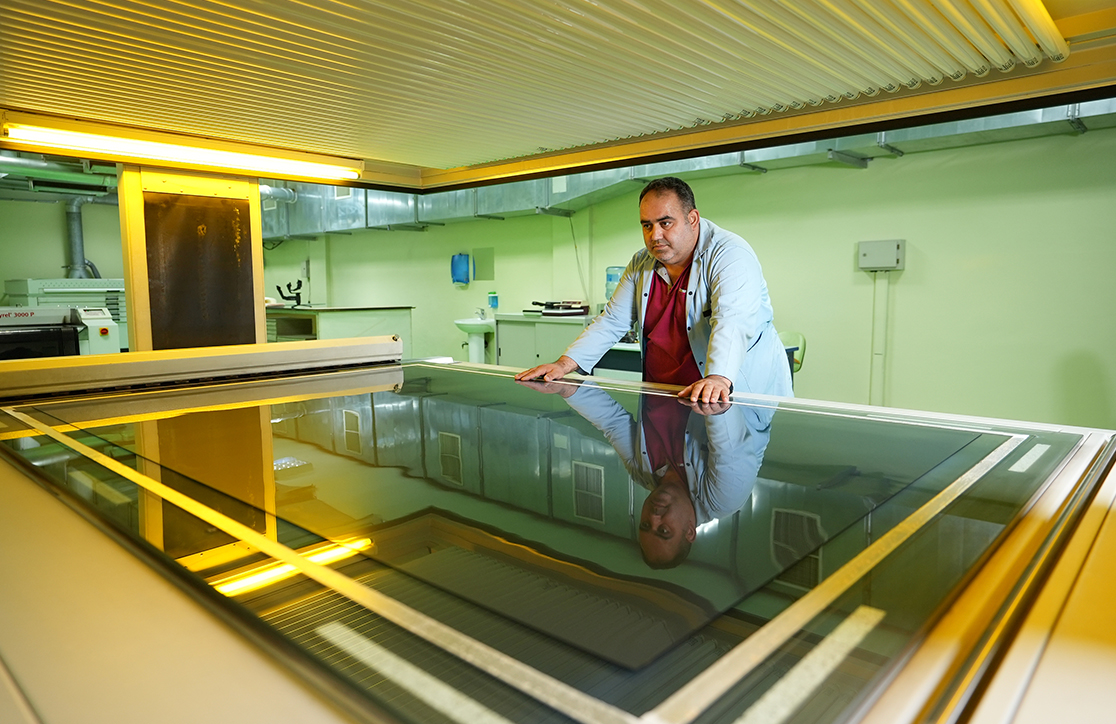
Extrusion
The first stage of the production phase; It is the production of PE and PP films with Blown and Cast Extrusion technology. The granular polymer gains its physical properties (thermal, optical, mechanical, size, color) at this stage. Today, KIMPACK, which has the most advanced possibilities of extrusion technology, can shoot in desired precision and dimensions (2 centimeters to 16 meters, thickness from 6 Microns to 2000 Microns), Mono or Coex (up to 7 times), with a capacity of 850 tons / day.
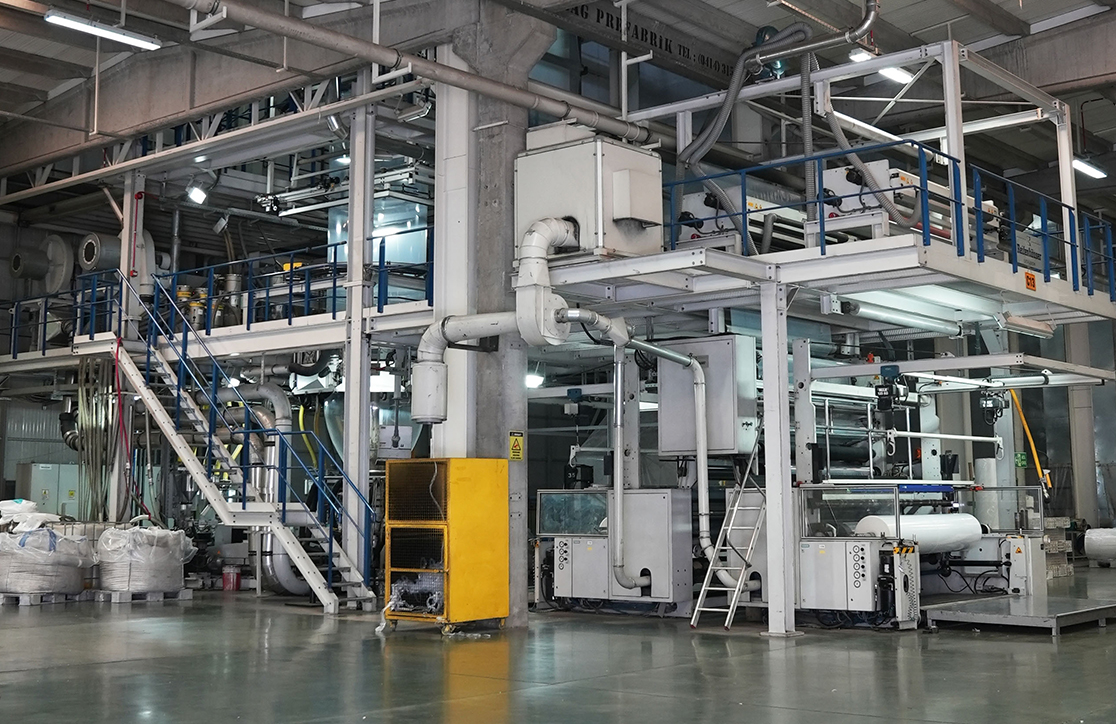
Printing
Up to 10 colors are printed with Flexso printing technique at KIMPACK and world-famous German Windmöller & Hölscher brand Astraflex, Novoflex and Miraflex machines are used. Especially as a result of developments in recent years, Flexo printing technique has caught Offset and Gravure printing technologies visually. In addition, thanks to its technology that allows the mold cylinders to be changed in a short time, an advantage is gained in lead times.
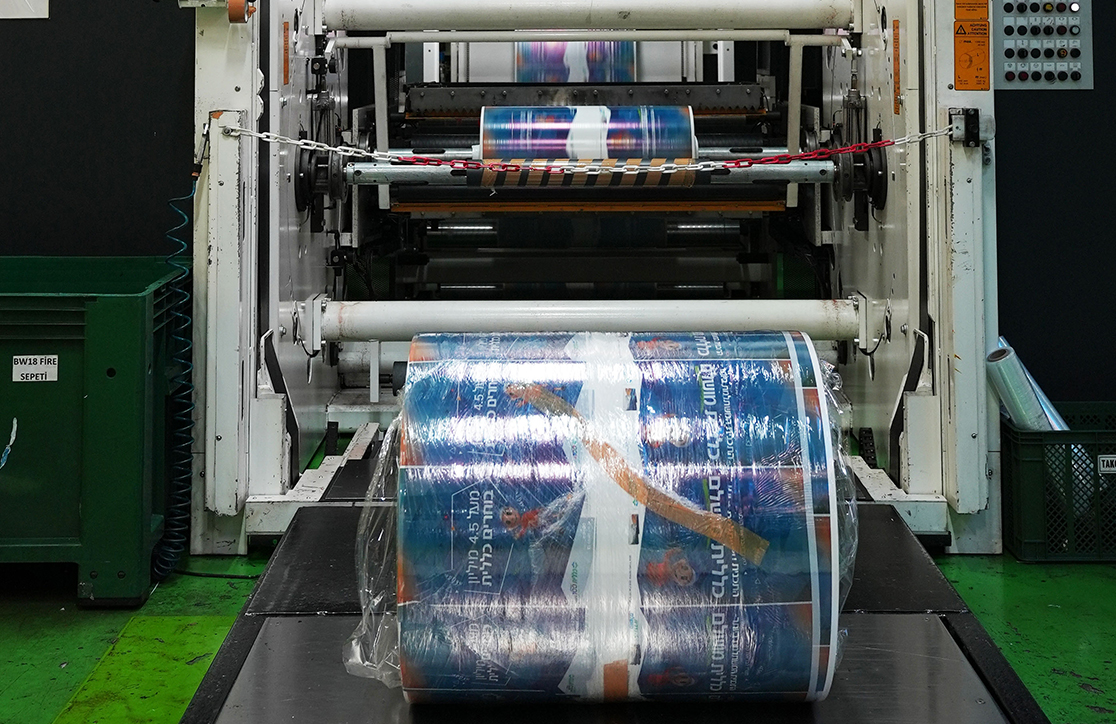
Lamination
Another method of producing material in the desired structure by creating a layered film from films of different properties is lamination. Printed or unprinted Aluminum, Polyethylene, BOPP, CPP and PET films are laminated to each other to produce visual, protective, durable permeable film. During this period, chemical lamination is made with KIMPACK, solvent-free glue with components in compliance with the food regulations. In addition, with the advantage of PE and CPP drawing lines, KIMPACK provides services in the field of lamination, especially in the production of PE / PE Packaging Films and BOPP / CPP Packaging.
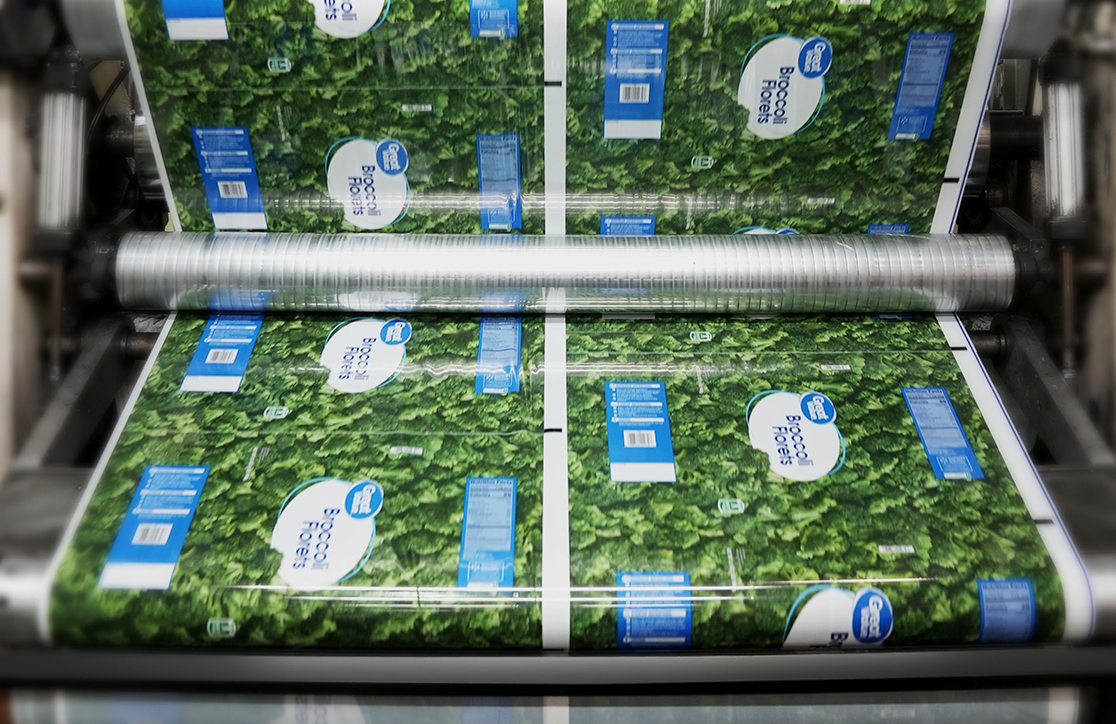
Garment
Plastic films in rolls are processed in cutting and slicing units with the latest technology in this section, such as baby diapers, bread bags, refrigerator bags, shirred diaper bags, soft-handled reinforced-athlete type bags and bags, hundreds of equal products that meet with the end consumer are turned into final products.
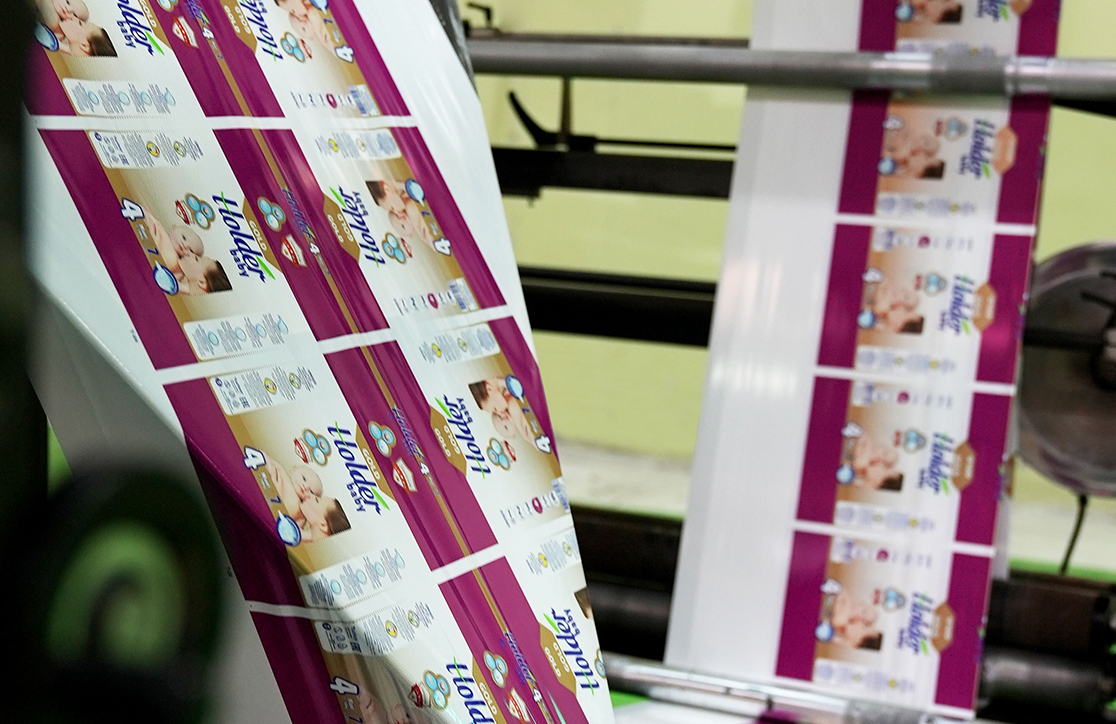